Case Study: Hydrostatic Locking - Hydraulic Hammering
A mounth ago, I wrote an article regarding the damages observed in piston connecting rods. Shortly after that, we received a service request from a ship where it was reported that the connecting rod had bent and fractured the liner. In this article, I will discuss the findings, conclusions and preventive measures related to the incident on the ship we provided service for.
![]() |
The piston rod that has fractured by striking the liner [1] |
We visited a ship waiting at anchor to inspect the situation of a diesel generator following an incident. Upon arrival we observed that all the cylinder heads had been removed by the ship's crew from the engine and that the engine could not be rotated. The damaged cylinders were numbers 2 and 6 (firing order 1-4-2-6-3-5). In these cylinders, the piston rods had bent and struck the liners resulting in fractures and the engine was immobilized in this state. The ship's crew had attempted to disassemble cylinder number 6 but had not succeeded. The piston of cylinder number 6 was partially elevated from the liner, as seen in the photo below.
![]() |
Piston No. 6 |
Two stuck pistons were eventually removed after a laborious effort. For connecting rods to strike and fracture the liners the rods must be bent or the liners must have been installed incorrectly during assembly where the liners are oriented in the wrong direction within the block. This is because some liners have recesses on their lower parts to ensure the rods do not come into contact with the liners. To ensure that the piston rods work along the axis of these recesses, the liners must be correctly positioned during installation. In the case of the ship in question, we found that the orientation of the liners was correct but both piston rods were bent.
![]() |
Bent piston connecting rod [1] |
Piston rod bending can occur due to factors like a seizure or the entry of a liquid into the combustion chamber, leading to hydrostatic locking which ultimately blocks the piston stroke. In this case, it's important to ascertain the extent of the damage and to identify the main cause that led to the bending of the piston rod by restraining the piston's movement. The images above illustrate a piston that has undergone plastic deformation due to its movement being hindered after the piston stroke was obstructed.
![]() |
The image of the broken liner after the piston was removed [1]. |
We mentioned that there should be two conditions for bending. One of these conditions is seizure, which were not observed on the crankpins and liners. Hardness testing and MPI (magnetic particle imaging) method were used to inspect the crankpins. No cracks were found, and the hardness was determined to be within the normal range.
![]() |
Crack testing on the crankpin - MPI [1] |
Hydrostatic lock, also known as hydraulic hammering, is a phenomenon that occurs in internal combustion engines when an incompressible fluid enters the cylinder preventing the piston from completing its stroke [2]. Hydrostatic lock happens when the volume of the fluid entering the cylinder is greater than the volume of the combustion chamber at top dead center. The force generated to complete the stroke exceeds the yield strength of the materials used in the engine causing damage to components like the piston rod [2]. This type of damage can be destructive and render the engine unusable [2].
One of the first substances that comes to mind as a cause of hydrostatic lock in a diesel engine is coolant or water. Issues related to coolant usually leave behind water-related traces. However in this specific engine we did not find the typical evidence associated with such problems. The ship's crew albeit belatedly, mentioned that there was a significant amount of oil on the upper part of the piston when the engine was disassembled. This information allowed us to redirect our focus more accurately. We began searching for signs of hydraulic lock caused by lubricating oil. We started looking for indications of oil-related hammering. One possible culprit that could cause excessive oil accumulation on the piston surface, surpassing the stroke volume, was the intake manifold. When we inspected the intake manifold, we indeed found an abundance of oil.
![]() |
Oil found in the intake manifold [1] |
The main suspect for the source of the oil found in the manifold was the turbocharger. When we disassembled all the pathways through which air enters the cylinder, we found oil. Finally, when we removed the intake filter of the turbocharger, we identified excessive clearance in the turbocharger bearings.
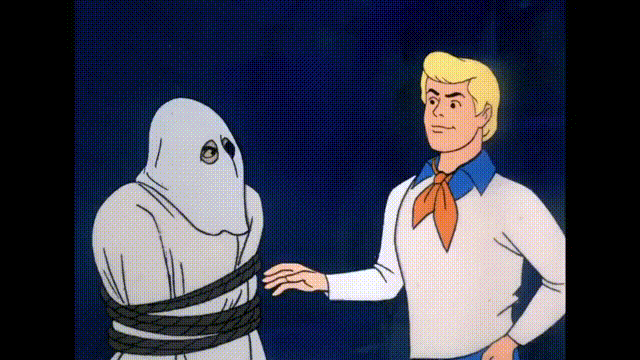
Since we couldn't gather information from the crew, we can't know exactly how the incident occurred. However oil from the turbine had filled the cylinders, and most likely, it caused damage during the initial startup. You can click on the link below to view the video showing the gap in the turbine bearings.
So, what can we do to prevent hydrostatic locking?
Almost every maritime company's engine start-up instructions include the opening of indicator valves and turning the engine a few revolutions before the initial start. This helps to evacuate any fluid present in the combustion chamber. By manually turning the engine with the pre-lubrication pump running any unwanted fluids accumulated in the cylinder can be detected. If there is any liquid accumulation inside it will signal us.
In addition to that regular monitoring of water tank levels will provide an indication of any decrease in the tank, which could signal a potential filling of the cylinder with cooling water.
Monitoring temperatures and oil pressures while the engine is running provides us with crucial information. Additionally, special attention should be given to engines that haven't been operational for a long time. Performing the procedures I've mentioned above along with the additional step of removing the turbine air intake filter to inspect the turbine can provide us with valuable insights.
Thank you for your valuable time.
Sources
[1] — Pictures taken by yours truly
[2] — DANLEY, Steven. Engine Hydrostatic-lock Mitigation. 2009. PhD Thesis. WORCESTER POLYTECHNIC INSTITUTE.
Yorumlar
Yorum Gönder